Increase OEE, reduce downtimes and boost profitability with TPM Pro manufacturing suite of solutions.
Know our solutions for electronic OEE measurementOur advantages
All the tools you need to get real time data from your machines
Wireless data acquisition devices and software applications to manage the factory floor, measure and conduct continuous improvement strategy. No third parties required.
Error free
Electronic data from the machines eliminate the use of printed forms so typing and transcription errors disappear. Information shows exactly what happens in the factory floor in a clear and easy way to understand.
People involved with productivity
TPM Pro creates empathy and a common language for everybody. OEE, Process States, Losses, Availability, Performance and Quality become in natural words that boost company's profitability.
Full visibility
TPM Pro OEE provides complete visibility of your entire factory and gives you reliable data needed for decision-making. Reports with multiple selection criteria are available with just a pair of clicks.
All the tools you need to get real time data from your machines
Wireless data acquisition devices and software applications to manage the factory floor, measure and conduct continuous improvement strategy. No third parties required.
Error free
Electronic data from the machines eliminate the use of printed forms so typing and transcription errors disappear. Information shows exactly what happens in the factory floor in a clear and easy way to understand.
People involved with productivity
TPM Pro creates empathy and a common language for everybody. OEE, Process States, Losses, Availability, Performance and Quality become in natural words that boost company's profitability.
Full visibility
TPM Pro OEE provides complete visibility of your entire factory and gives you reliable data needed for decision-making. Reports with multiple selection criteria are available with just a pair of clicks.
Get focus
Tree of Losses Multi Level Pareto shows clearly which loss to attack first and may give you a quick idea about return of investments when valorised.
Best Benefit – Cost ratio
Both our small and large solutions have a payback in less than 6 months. TPM Pro gets big savings increasing production output and improving the use of resources.
Data is only yours
You are the owner of the data base and there are no risks to be seen by anyone else at least you wish to share it. Then, data and reports can be accessed from any device trough internet or intranet.
A solution for each type of requirement
Fully scalable system lets you start with a simple, plug and play solution to make a pilot test, and reach to a complete customized solution that may include ERP/EAM/APS integration.
Get focus
Tree of Losses Multi Level Pareto shows clearly which loss to attack first and may give you a quick idea about return of investments when valorised.
A solution for each type of requirement
Fully scalable system lets you start with a simple, plug and play solution to make a pilot test, and reach to a complete customized solution that may include ERP/EAM/APS integration.
Best Benefit – Cost ratio
Both our small and large solutions have a payback in less than 6 months. TPM Pro gets big savings increasing production output and improving the use of resources.
Data is only yours
You are the owner of the data base and there are no risks to be seen by anyone else at least you wish to share it. Then, data and reports can be accessed from any device trough internet or intranet.
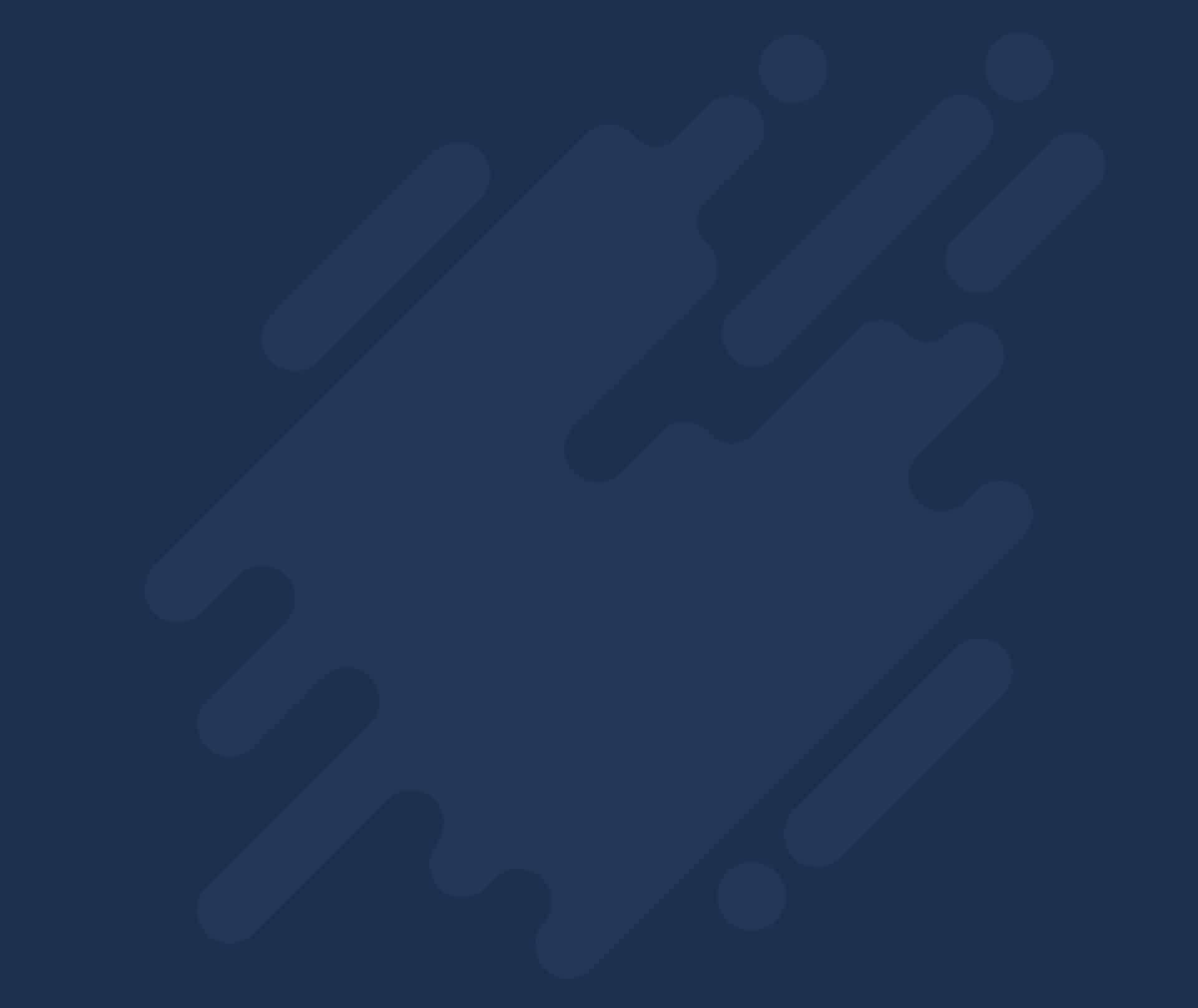
Testimonials
Jorge Neira Robles
Projects Leader, Duferco Group
Jorge Neira Robles
Projects Leader, Duferco Group
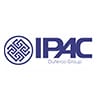
Eng. Claudio Giuliani
Head of Corporate Production Control in Alicorp S.A
Eng. Claudio Giuliani
Head of Corporate Production Control in Alicorp S.A
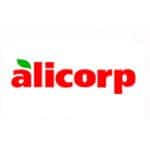
Eng. Gabriela Meiller
Director at Abbott Laboratories
Eng. Gabriela Meiller
Director at Abbott Laboratories
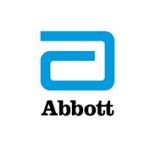
Eng. Sebastián Bonica
Director at UNILEVER
Eng. Sebastián Bonica
Director at UNILEVER
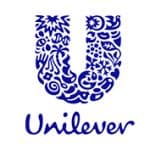
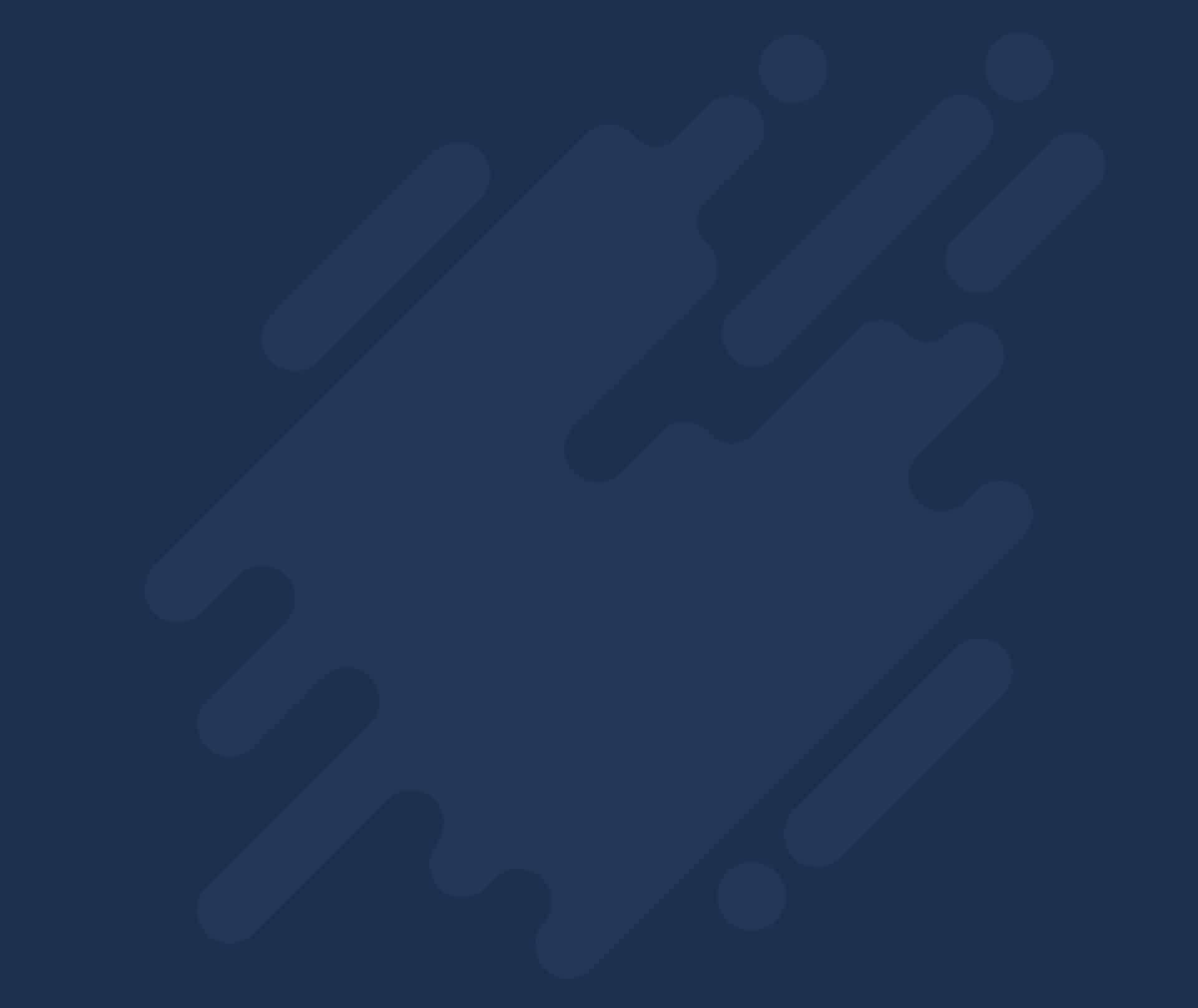
Testimonios
It is an excellent tool! You can get a lot of juice. Causes of losses are quickly identified and displayed to take corrective actions.
Eng. Sebastián Bonica
Director at UNILEVERProductivity losses were always close to our eyes and we didn't see them. Now with TPM PRO OEE we see the losses, identify them, value them and act accordingly to eliminate or minimize them. Then we monitor them and see how they evolve over time.
Jorge Neira Robles
Project Leader Duferco GroupWe use it every day to detect opportunities for improvement. Personally, it makes the work of preparing management reports very easy for me.
Eng. Claudio Giuliani
Head of Corporate Production Control in Alicorp S.AWe obtained important improvements in Operational Efficiency. The implementation of KPI Monitor helped us to increase the OEE of the production lines almost immediately.
Eng. Gabriela Meiller
Director at Abbott Laboratories
Why to use an OEE system?
Productivity losses are present in all industrial processes. Often the root cause of the problems that disturb the processes is unknown, and sometimes losses are minimized. A system that measures OEE electronically unmasks productivity losses and makes it possible to measure real performance of the machines, since it measures production (machine speed) minute by minute and compares it against a standard. It eliminates manual data entry and its subsequent load into spreadsheets. Avoid mistakes and present the necessary information to make immediate executive decisions.


Why to use an OEE system?
Productivity losses are present in all industrial processes. Often the root cause of the problems that disturb the processes is unknown, and sometimes losses are minimized. A system that measures OEE electronically unmasks productivity losses and makes it possible to measure real performance of the machines, since it measures production (machine speed) minute by minute and compares it against a standard. It eliminates manual data entry and its subsequent load into spreadsheets. Avoid mistakes and present the necessary information to make immediate executive decisions.
Amount of produced parts and the elapsed time are recorded and visible in real time. Electronically, using sensors connected to our Wireless Data Collectors, times and number of produced parts are determined.
Acquired data is then converted into useful information with the help of an operator that simply performs manual data entry. Operators inform about change of products, stoppages, defective parts, lots, with just a pair of clicks.
The system analyses gathered data and reports:
- Availability (stoppages and other losses that reduce the available time)
- Performance (machine or line speed and minor stoppages)
- Quality (good and rejected parts by defect)
First, it is increased by the fact of beginning to electronically control the processes and then by the application of Continuous Improvement methodologies guided by the KPIs (Key Performance Index) that it presents in real time.
None of our customers experienced an increase of less than 10% increase in Productivity (measured by OEE) and in most cases the increase reached more than 20% in one year. In all cases, the ROI (Return on Investment) occurred before 6 months.
Mass production is usually the easiest to control since in these processes there are always sensors that measure what has been produced. For example, packaging or bottling lines, packaging processes, machines or high production lines, etc.
Batch processes can also be controlled, provided there is an electrical signal that indicates their operation. The more automated the process, the easier to measure and control. It is not the right system to measure the efficiency of manual processes.
In general, all machines or production lines already have a sensor that delivers that electrical signal (counter). It can be an optical, inductive type sensor, a relay contact, or taken from an output of a PLC or other control or counting device. Any of these alternatives is useful to use as a digital input to our Data Collectors.
In TPM Pro we have a lot of experience in connecting many different types of processes. Some of them are easy and others give a little more work and even in some cases require some special sensor that we can provide. The capacity of our Data Collectors allows to combine several inputs and create different logics to indicate the operation of the machine or the production of a unit.
Electronic devices such as PLCs are more dedicated to sequencing the operation of the line and controlling some of its variables. Although they were not designed for productivity measurement, a correct programming of them could achieve it. However, PLCs are normally embedded in the production line, and therefore, programming or reprogramming these devices generates downtime and can cause malfunction of the line if an error is made, with the consequent loss of the manufacturer's warranty.
Likewise, the current control devices are wired, most of them with a RS 232/422/485 serial connection or, in the best case, they use a socket from the LAN network. These wiring are always expensive because they require cable streets, work at height, distribution boxes, special mesh to eliminate electrical noise, etc. TPM Pro ZB Wireless Data Acquisition devices solve all these problems from end to end:
- They are Plug & Play
- They do not interfere in the programming of the line (it is outside)
- No wiring required
- Communications do not produce interference or suffer from electrical noise.
- They are cheaper than a conventional PLC.
- There is no need to deal with different manufacturers / device models.
They do it through the TPM Workstation application, which also allows them to know some results of their work, the list of WOs that they must perform and presents all the associated documents related to the current WO (control plans, checklist, plans, configuration sheets, 1 point lessons, etc.).
The way to report or declare news is extremely easy and intuitive. The operator selects the type of declaration and reports the loss.
The TPM Pro workstation is ready for use on both common PCs and industrial tablets with touch screens. Its large buttons and the logic of the declaration allow the information in seconds.
However, the following clarification is valid here:
Even when the line had a high technological level, automatic stop coding is not recommended because in all cases the information is not enough. For example: a sensor of lack of packaging material could indicate that the line is stopped for this reason… .but why am I missing packaging material? There the reasons can be varied and for the purpose of a good coding of the Losses they should be divided into problems of logistics, supply, defective materials, breaks or blockages of the feeder, failure in the sensor, etc.
The integration is done bi-directionally, that is, it receives information from the ERP as the Work Orders (WOs) that must be made and TPM Pro returns the result of those WOs at regular intervals or on demand.
This avoids the duplication of data entry, eliminates errors by omission, by typing and by transcription; while the ERP may properly calculate the cost of a production order, know the consumption of raw materials minute by minute, etc.
Likewise, the programming of the production in execution time, corrects the probable errors in which the ERP incurs because it does not know the current state of the lines when launching the MRP run.
Amount of produced parts and the elapsed time are recorded and visible in real time. Electronically, using sensors connected to our Wireless Data Collectors, times and number of produced parts are determined.
Acquired data is then converted into useful information with the help of an operator that simply performs manual data entry. Operators inform about change of products, stoppages, defective parts, lots, with just a pair of clicks.
The system analyses gathered data and reports:
- Availability (stoppages and other losses that reduce the available time)
- Performance (machine or line speed and minor stoppages)
- Quality (good and rejected parts by defect)
First, it is increased by the fact of beginning to electronically control the processes and then by the application of Continuous Improvement methodologies guided by the KPIs (Key Performance Index) that it presents in real time.
None of our customers experienced an increase of less than 10% increase in Productivity (measured by OEE) and in most cases the increase reached more than 20% in one year. In all cases, the ROI (Return on Investment) occurred before 6 months.
Mass production is usually the easiest to control since in these processes there are always sensors that measure what has been produced. For example, packaging or bottling lines, packaging processes, machines or high production lines, etc.
Batch processes can also be controlled, provided there is an electrical signal that indicates their operation. The more automated the process, the easier to measure and control. It is not the right system to measure the efficiency of manual processes.
In general, all machines or production lines already have a sensor that delivers that electrical signal (counter). It can be an optical, inductive type sensor, a relay contact, or taken from an output of a PLC or other control or counting device. Any of these alternatives is useful to use as a digital input to our Data Collectors.
In TPM Pro we have a lot of experience in connecting many different types of processes. Some of them are easy and others give a little more work and even in some cases require some special sensor that we can provide. The capacity of our Data Collectors allows to combine several inputs and create different logics to indicate the operation of the machine or the production of a unit.
Electronic devices such as PLCs are more dedicated to sequencing the operation of the line and controlling some of its variables. Although they were not designed for productivity measurement, a correct programming of them could achieve it. However, PLCs are normally embedded in the production line, and therefore, programming or reprogramming these devices generates downtime and can cause malfunction of the line if an error is made, with the consequent loss of the manufacturer's warranty.
Likewise, the current control devices are wired, most of them with a RS 232/422/485 serial connection or, in the best case, they use a socket from the LAN network. These wiring are always expensive because they require cable streets, work at height, distribution boxes, special mesh to eliminate electrical noise, etc. TPM Pro ZB Wireless Data Acquisition devices solve all these problems from end to end:
- They are Plug & Play
- They do not interfere in the programming of the line (it is outside)
- No wiring required
- Communications do not produce interference or suffer from electrical noise.
- They are cheaper than a conventional PLC.
- There is no need to deal with different manufacturers / device models.
They do it through the TPM Workstation application, which also allows them to know some results of their work, the list of WOs that they must perform and presents all the associated documents related to the current WO (control plans, checklist, plans, configuration sheets, 1 point lessons, etc.).
The way to report or declare news is extremely easy and intuitive. The operator selects the type of declaration and reports the loss.
The way to report or declare news is extremely easy and intuitive. The operator selects the type of declaration and reports the loss.
However, the following clarification is valid here:
Even when the line had a high technological level, automatic stop coding is not recommended because in all cases the information is not enough. For example: a sensor of lack of packaging material could indicate that the line is stopped for this reason… .but why am I missing packaging material? There the reasons can be varied and for the purpose of a good coding of the Losses they should be divided into problems of logistics, supply, defective materials, breaks or blockages of the feeder, failure in the sensor, etc.
The integration is done bi-directionally, that is, it receives information from the ERP as the Work Orders (WOs) that must be made and TPM Pro returns the result of those WOs at regular intervals or on demand.
This avoids the duplication of data entry, eliminates errors by omission, by typing and by transcription; while the ERP may properly calculate the cost of a production order, know the consumption of raw materials minute by minute, etc.
Likewise, the programming of the production in execution time, corrects the probable errors in which the ERP incurs because it does not know the current state of the lines when launching the MRP run.